-
-
Notifications
You must be signed in to change notification settings - Fork 22
Bed Heater
LH Stinger PI Bed heater Installation
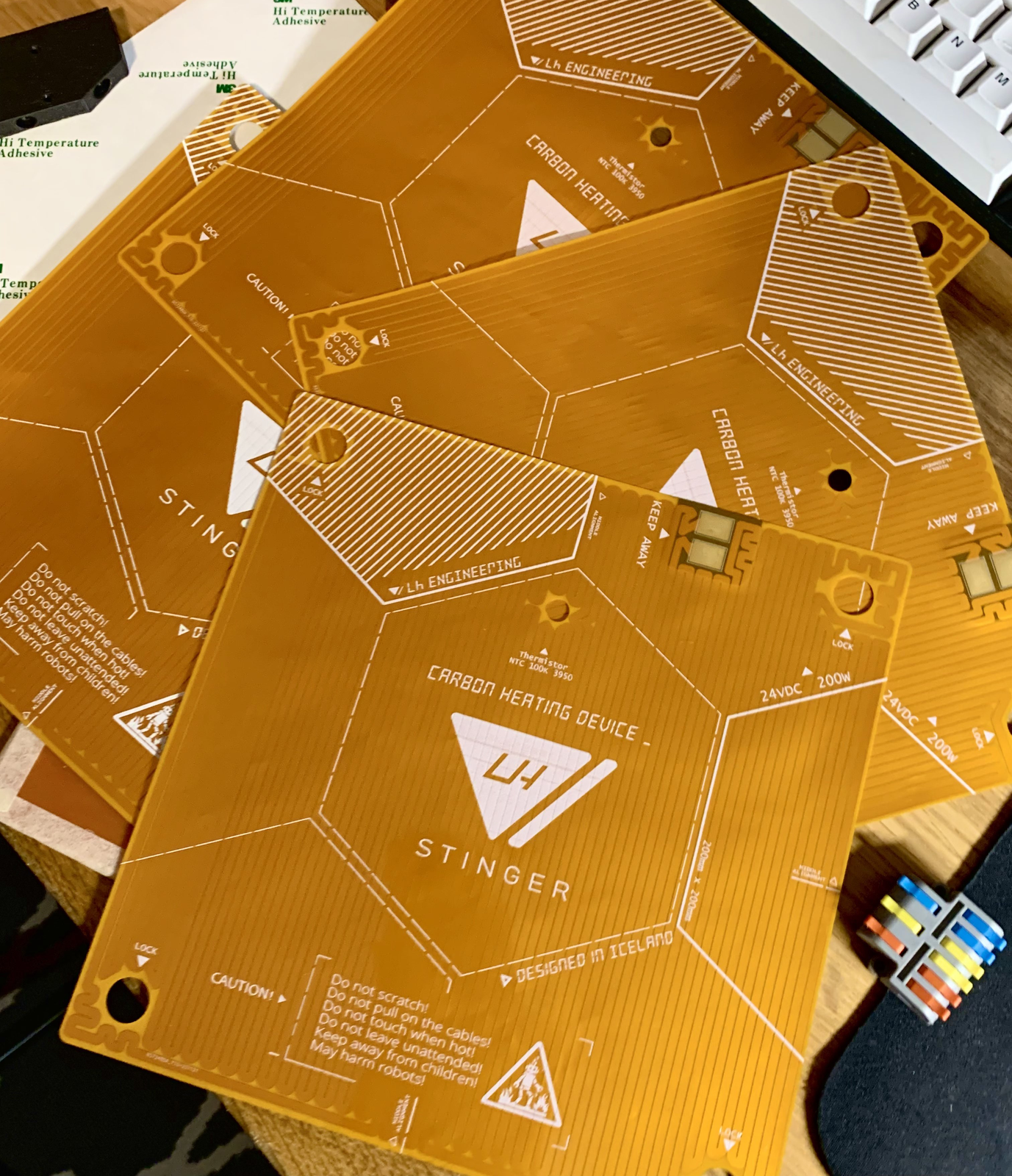
This guide covers the steps required for soldering and installing the PI flex PCB heater.
Important
Please ensure you read the Safety section of this guide.
Disclaimer
This is a DIY (Do-It-Yourself) experimental project. This PCB is provided "as is" without any guarantees or warranty, and is not certified for any commercial or critical applications. Use it at your own risk. The creator assumes no liability for damages or injuries resulting from its use, including but not limited to fire, electric shock, personal injury or property damage. By using this PCB, you agree to the terms of this disclaimer.
Warning
Please adhere to the following safety guidelines:
- Professional Guidance: Pay close attention to the instructions and seek help from a qualified professional if needed.
- Unattended Operation: Do not leave the heater running unattended.
- Component Safety: Ensure no other components are close to rubbing or touching any parts of the PCB.
- Electrical Conductivity: Carbon Fiber has high electrical conductivity. Any damage to the PCB can cause a short circuit and potentially start a fire.
- Liability: The author of this guide, and other affiliates, are not responsible for any damage caused by the items and instructions listed here.
- Use an appropriate soldering iron capable of delivering and sustaining 400C.
- The process should be done as quickly as possible, exposing the components to heat for the shortest duration possible.
- If something doesn't work out. Let things cool down, evaluate your approach and try again.
- Don't insert a cold wire into a pool of solder, and don't apply a pool of solder on a cool component. This will result in a cold solder that will break apart with time.
- Clean the parts with isopropyl alcohol before and after, and use plenty of flux.
- A 16 AWG or thicker motion rated cable is required for the main bed power delivery.
- Don't move the bed if the cables are not properly attached with a strain relief.
- Use heat shrink tubing and remember to pre-load it onto the cable before soldering.
- Test the components for shorts before and after the installation. Ensure that there is no conductivity between the heater wires and the carbon fiber plate.
- Don't use the heater at temperatures over 110C.
Note: If you are planning to use the LHS Breakbeat - breakout board, then you will need to solder a XT60U Male connector.
- Insert the heat shrink tubes.
- Clean and apply flux to the surfaces.
- Tin the power cable and fill the XT60 connector with solder.
![]() |
---|
- Heat up the pool of solder inside the connector and the wire. Alternate between each other.
- Insert the wire into the solder terminal, and keep applying heat for two seconds.
- The temperature in the connector is very high, so let it cool for a while before continuing with the other side.
![]() |
---|
- Heat up and secure the heat shrink.
![]() |
---|
![]() |
- Clean the pads with isopropyl alcohol.
![]() |
---|
- Add flux to the pads.
![]() |
---|
- Heat up the pads and then apply solder until a pool is created.
Spending too much time heating up the pads might damage the PI sheet and adhesive. - Let the surfaces cool down to room temperature.
![]() |
---|
- Heat up the wire separately until the solder starts melting.
- Start heating up the pad.
- When the solder starts becoming liquid, alternated between heating up the wire and the pad.
- Insert the wire into the solder pool, apply heat for two seconds and keep holding until the solder cools down and solidifies.
- Let everything cool down to room temperature before proceeding with the other pad.
- Make sure there is enough gap between the solder joints.
- Clean up the surfaces with isopropyl alcohol.
![]() |
---|
- Clean the surfaces and apply a layer or two of Kapton tape.
![]() |
---|
- Verify the continuity of the circuit by testing the end of the cable with a multimeter.
- Now the heater is ready to be glued onto the carbon fiber bed.
![]() |
---|
- Clean up the CF bed surface with isopropyl alcohol and make sure not to touch it with bare fingers.
- Use the Bed Heater Alignment Jig for mounting the heater.
https://github.com/lhndo/LH-Stinger/blob/main/STL/Other/Bed%20Heater%20Alignment%20Jig.stl - Place the CF bed with the screw holes into the alignment pins (1). The top side of the bed should face downwards.
![]() |
---|
- Start by peeling off a bit of the adhesive from the edge opposite of the one with the wire pads and insert it into this gap.
- The alignment lines (2) should help you mount the heater precisely.
![]() |
---|
- You can find an overview of the process in the video below: https://www.youtube.com/shorts/Hy14AWyfAY4
- Clean up the surface with isopropyl alcohol
- Add a blob of thermal paste onto the carbon fiber through the round opening.
- Insert the glass bead thermistor into the thermal paste.
![]() |
---|
- Cover the area with Kapton tape to secure the thermal paste and thermistor.
![]() |
---|
- Secure the cable with Kapton tape towards the location of the cable strain relief
![]() |
---|
Caution
- Ensure that there is no conductivity between the heater wires and the carbon fiber plate. Test with a multimeter!
- Carbon Fiber has high electrical conductivity. Any damage to the PCB can cause a short circuit and potentially start a fire.
- When mounting the bed onto the carriage, ensure that no other components like screws are close to rubbing or touching any parts of the PCB.
If you find that the gap is not sufficient for safe operations, add some washers/spacers to increase the distance between the bed and the carriage. - Do not leave the heater unattended and have a smoke detector in the vicinity of the printer.
- The heater adhesive will cure itself in 24h at room temperature.
- Afterwards, start running a few gentle heat cycles, and in the end perform the PID tuning.
For an accelerated method that takes 5 to 6 hours, you can follow to process below.
The following procedure is described by Róbert Lőrincz
Caution
Piercing the heater to remove air bubbles is absolutely not recommended! The traces are very close to each other and there is a very high chances of shorting the traces against the carbon fiber surface!
- Set temperature to ~40°C degrees and leave it at 40°C for about 2 hours.
- Increase temperature to 60°C, let it for about 2 hours.
- Increase temperature to 80 degrees, let it for about 2 hours.
- You’re done, let It cool down and perform PID tuning.